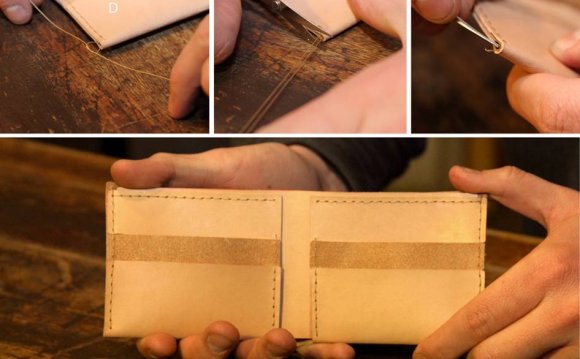
It is quite possibly the simplest form of wallets. Though make no mistake, it still takes a few steps and a couple of tricks to get it looking just right. In this tutorial I have photographed every step in making this leather wallet from figuring out the dimensions, to preparing the edges, dyeing, and hand stitching. If you have been following along in the past month or two you may have seen my leather belt tutorial as well, it’s worth checking out after you stitch this little guy together. Since this is a fairly long post (~ 100 photos), I am going to jump right to it. Give yourself almost 2 hours if this is your first project.
Above are all the essential tools required for this wallet. From left to right: Steel ruler, wax pencil, rolling cutter, edge creaser, stitching groove cutter, edge beveler size 0, 6 diamond shaped hole punch, scissors, two hand sewing needles, waxed thread, stitching pony (I built this one myself, but you can buy them online pre-made). Up top I have a rubber pounding mat to absorb the punch later on.
The type of leather I am using is called vegetable tanned. It is a type of tanning that allows me to work with the leather, mark it, and dye it. I chose a scrap 3-4 oz. piece that measured more towards the 3 oz. side – meaning it’s a bit skinny.
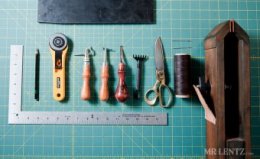
The first thing you will need to do is create your pattern, I already have mine set up, but let’s take a look at how to make one for this wallet. First – grab some posterboard and measure out a rectangle 9.5 inches long and 4.25 inches wide.
Then measure and mark the two fold lines. The distance between them needs to be 7.75 inches in order for a dollar bill to fit in with the card and only be folded once. To cut the angles as I have – use the photo as reference for marking the lines, but don’t take off too much! We need enough leather to grab the cards when it is all stitched up.
Lay your template down on the leather and mark up the leather. I try to minimally mark the leather only where I know that I will need reference points. This keeps the wax pencil from getting everywhere.
I cut out the leather with my rolling cutter and steel ruler.
Lay the leather flesh side up (that’s the rough side) and mark the fold lines.
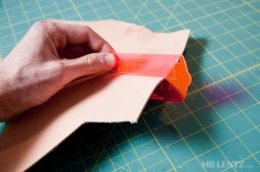
Then wet the entire length of the fold with a little bit of water. Not much water is needed – this just ‘cases’ the leather and allows it to be formed and hold its shape when you bend it.
Go ahead and bend both sides straight across. I also use a lightweight mallet to help pound down the fold.
Next we need to prep the grain side of the leather (smooth side) for edge marking. Wet the grain side very lightly, covering the entire piece. If you only wet certain sections – that area of leather will actually be slightly darker once everything dries.
Run the edge marking tool down both short ends of the leather, starting and stopping about 1/4 inch from the edge. I like adding this accent to give the piece a tiny bit of extra detail.
In order to give ourselves a good straight reference line for stitching…as well as help sink the stitching into the leather thus protecting it – we need to use a stitching groove cutter. Set yours so the middle of the hole to the inside edge of the cylinder is about 4mm.
In the photo above you can see that I started and stopped the groove just after the fold we made previously. Whatever is above the fold will be on the inside of the wallet…and with the groove – it is sometimes hard to get it to line up with the stitches on the inside, so I end it short.
The edge beveler is a great tool – and for quite a while I was using the wrong one! I recently purchased the smallest size I could find from Weaver Leather Supply, a size 0. This is a perfect size for thin leathers such as our 3-4 oz.
The edge beveler takes off the corner edge and helps the appearance of rounding it. In general, these small touches go a long way to getting your leather work to look really nice – so it’s worth the effort.
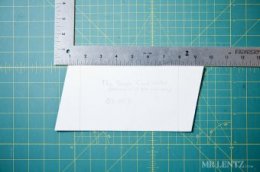
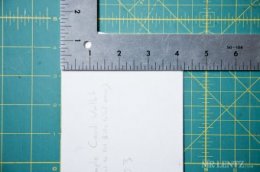
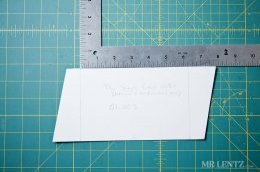
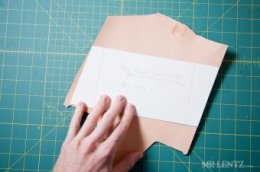